My Story
The concept of flexitanks originated during World War II when large flexible bladders were used to transport both water and fuel in key battlefield support environments. These early tanks were made from layers of fabric sandwiched between layers of rubber. This basic design continued to be used in slowly evolving versions by the US military well into the 1960’s. Transitioning into the 1970s, shippers in the UK implemented this flexitank technology to transport various non-hazardous liquids in containers via ocean freight. These early forms of flexitanks allowed for cost savings versus shipping ISOTank containers, but they were often difficult to work with, required significant cleaning, and were used multiple times. I had my first experiences with these first generation of flexitanks circa 1993–1994-time frame. All went well until I experienced a catastrophic leak at the port of Charleston and the owner of my company called to suggest that maybe I shouldn’t ship those anymore.
Moving forward into the 2000’s we saw not so much an evolution, but more of a revolution in flexitank design. Gone were the reusable tanks in favor of a single use, fully recyclable version, multi-layer tank made of 2 or more inner layers of polyethylene and a protective outer layer of woven polypropylene. These tanks are designed to travel in 20’ containers and require first quality containers without any damage to the corrugated metal walls. Additionally, this basic design requires a metal bulkhead at the back of the container to protect the doors from damage by a surging flexitank. Based on this modern design the use of flexitanks has been expanding year over year for the last 20 years.
How About Refrigerated?
Going back to 2012 timeframe I met with a flexitank manufacturer to explore the idea of a flexitank that could be used in a reefer. The initial discussion revolved around the thought of using a 20’ Reefer. This option presented two main challenges that were nearly insurmountable.
1. The walls of a reefer are made of a layer of insulation sandwiched between two thin layers of metal. These walls are exponentially weaker than the corrugated steal of a standard container. Because of this design feature, the flexitank could not press against the walls as they do in a standard container as they would simply bust the walls out.
2. If using a 20’ reefer the flexitank itself would have completely covered the “T Floor” thereby blocking proper air flow which would have compromised the cooling (or heating) of the container thereby negating the use of the reefer.
Neither issue was seen as surpassable, and the industry went back to the drawing board.
A handful of manufacturers kept working on this challenge and came upon the idea to use a 40’ reefer instead of the 20’ option. By using a 40’ reefer, the flexitank could ride low in the container and be designed to not touch the walls or the doors of the container. These initial tanks were created to be around 37’ in length and the initial testing was promising. However, upon more stringent road and ocean testing we discovered that the motion of the container while in transit generated significant waves in the flexitank, these waves in turn caused microtears in the inner layers which of course led to leaking. The next challenge then was to engineer a way to stop the waves and the resulting tears and leaks.
3-Tank Solution
The solution taken by most manufacturers was to place baffles inside the flexitank essentially creating multiple chambers inside the long flexitank. The good news is that the baffles worked to eliminate the tears, the bad news is that the chambers these baffles created held on to the product making it difficult to discharge the flexitank at destination. This resulted in a reduced yield of product in the range of 94%. To put it another way there was around 6% of product trapped inside the flexitank. This heel / residue was essentially thrown away and that resulted in reduced profitability. In a 24,000-liter flexitank that would result in around 1,440 liters (380 gallons) of lost product.
The other solution to the 40’ reefer question was to use 3 separate smaller tanks. The results of the tests for the three tank options were simply superior. The wave action issue was eliminated leading to riddance of tears. The three smaller tanks were easy to handle by a single person versus the larger single tank option which requires multiple people to load and remove from the container. We have found over several years of shipping the 3-tank system that our standard yield is + 99%. When using 3 x 8,000-liter tanks that translates into 240 liter (63 gallons) or less of heal / residue. Lower waste equals greater profitability.
Global Supply Challenges
In the past several years we have seen the global fleet of 20’ containers degrade to a fairly rough shape. Obviously, you do not want to put a standard flexitank into a 20’ container that is in bad shape with dents, damage and the resulting sharp edges that will damage the flexitanks in transit. Further, we have found that the more recently manufactured 20’ containers are not as high quality as previous generation containers, and the walls often bulge when loaded with a larger 22,000 - 24,000-liter flexitank. By using a 40’ container the flexitanks never touch the walls, or the door, of the container, thereby eliminating the issue with bulging.
The final benefit we find with using the 3-tank system is the readily available nature of 40’ containers across all ports. New Orleans, for example, often has limited to nonexistent supply of 20‘ containers. More times than I care to recall I have had product miss vessels because of the lack of 20’ equipment in New Orleans and Mobile. The 3-tank system essentially eliminates this problem.
Why Not The Road?
Once we had some experience in shipping these tanks in ocean reefer containers, the idea came to try them in domestic over the road 53’ trailers. For long cross country moves of liquids, the cost of using the 3-tank system was significantly lower than tanker trucks for the same moves. The tanks performed equally well in either refrigerated domestic trailers or standard dry trailers. The same thing is true for use in standard 40’ dry ocean containers.
The Future Across Industries
I recently attended a Bulk Wine Expo in the San Francisco area. A speaker at the event acknowledged the issues for flexitanks in 20’ containers that I have outlined above. Then he spoke on the 40’ container flexitanks option and addressed the issue with 94% yield, but he did not address the availability of the three-tank system. His company does not offer the three-tank system so this is not surprising, but why not? We know the technology is out there and we have it. The other benefit to the wine industry is the ability to move higher quality wines at constant “cave” temperature between 55-60° Fahrenheit. The wine will neither “cook” nor freeze in transit. Our 3-tank system is perfect for bulk wine moves for this reason.
As we move forward, the 20’ container fleet will continue to age out and be replaced with lower quality containers. The next evolution of flexitanks is represented by the three-tank system and will likely eventually match the volumes of the 20’ standard options.
ASF- The Human Standard in Global Logistics
ASF Logistics, founded 24 years ago, began with a singular idea: to put people-first and bring integrity and honor to the global freight forwarding market. Every human interaction is an opportunity to create a positive impact. Beginning with the simple act of fostering transparent, respectful dialogues and responding promptly to client needs. This strong belief system has positioned ASF as a trusted logistics partner and important resource for industry-leading logistics technology. Our collaboration with Gnosis Freight, a Container Lifecycle Management technology provider and leader in data integrity, positions ASF on the cutting-edge of logistics technology today.
While technology plays a pivotal role, it is the human element at ASF that ensures the agility, resilience, and success of supply chain operations, especially in this ever-changing global trade landscape.
ASF Logistics provides supply chain logistics services throughout the world including all forms of transport, cargo insurance, customs brokerage, and contract management. Specializations include: Flexitanks, reefer logistics, and project cargo.
Meet Our Expert
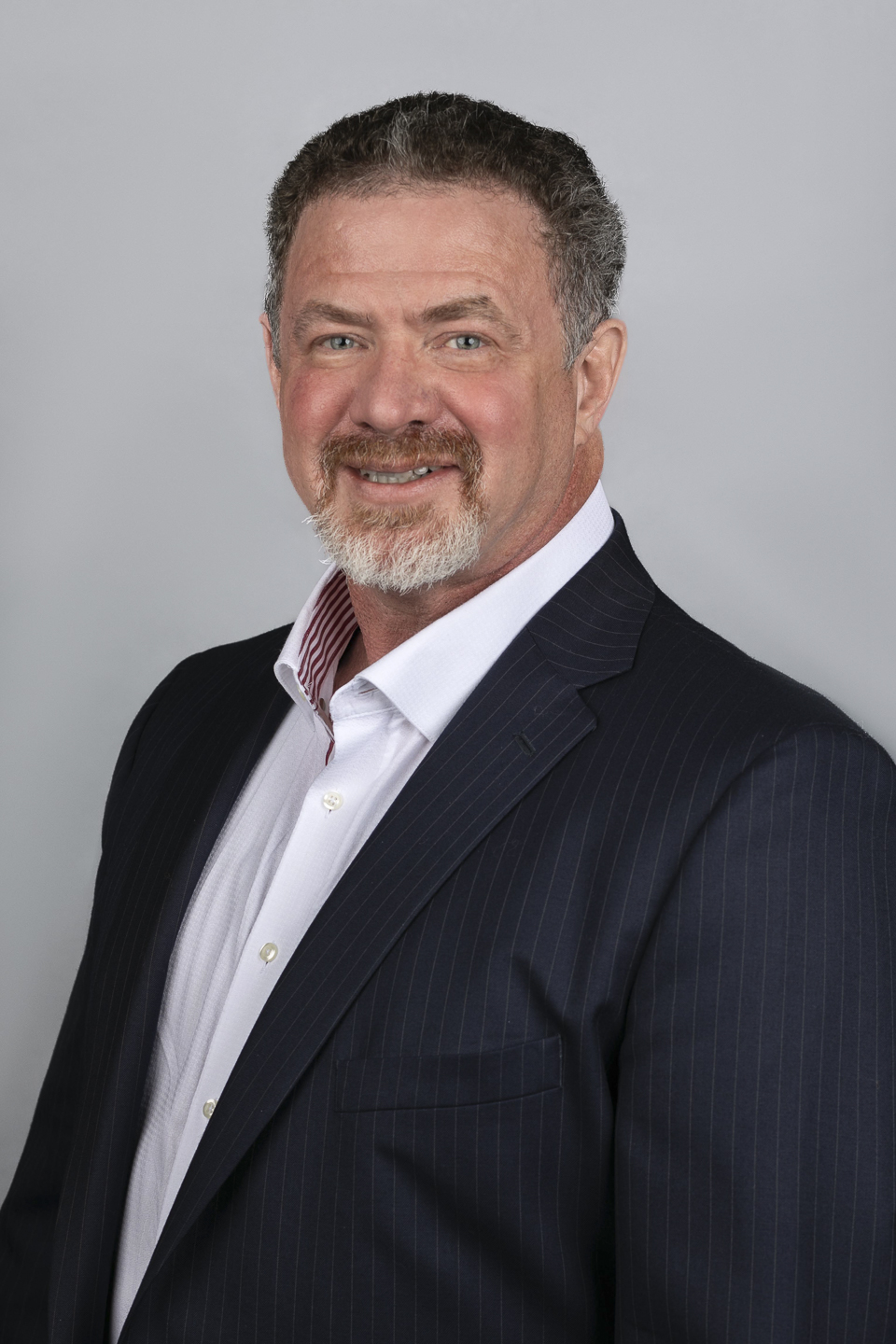
This article is reviewed by Jeffrey D. Plumley, Chief Commercial Officer and Licensed US Customs House Broker.
Jeff has an extensive background in global logistics, spanning various freight forwarding executive management positions. As a Licensed US Customs House Broker, he has managed regulatory compliance and is a worldwide expert in Flexitank transportation logistics.
In addition to his strong forwarding and Flexitank background, Jeff was also Head of Regulatory Compliance and Sales for a major global logistics software provider. He has over 30 years of logistics experience and a strong leadership background having graduated from the Citadel.